The Auckland innovators have developed automated mussel and scallop openers, and vision inspection systems for detecting faults in wine labels, infant formula cans and bottles.
KanDO made automation systems for putting handles on the neck of plastic bottles and lowering 28 metre-high light poles in Doha, Qatar. Now, kanDO has big hopes for its Guardian Bandsaw project which minimises the risk of injuries in meat processing plants and other workplaces.
The company developed an unprecedented safety system that is being used in meat processing plants in New Zealand, Australia and the United States.
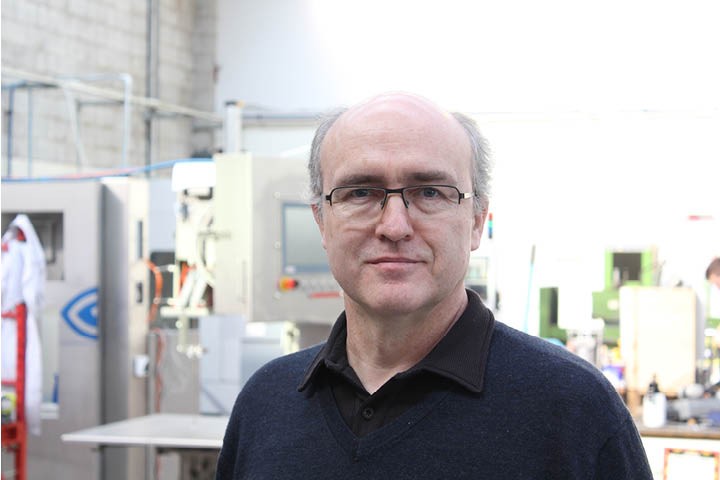
Guardian improves safety culture
KanDO's team of designers and engineers designed and built the Guardian machine which is a purpose-built bandsaw with an advanced vision detection system. The Guardian dramatically improves the safety culture in the boning room of the meat processing plants, and also the quality of the cuts made.
The kanDO system detects the operator's hand when it gets close to the blade and immediately shuts down the bandsaw, preventing serious injury. The vision system recognises the blue food-grade gloves worn by the operators and should they come within 40mm of the blade, the Guardian braking system is triggered and the bandsaw stops within milliseconds.
KanDO has proven that the operator's hand doesn't have a chance of making contact with the blade. The co-founder of kanDO Niven Brown says "we can stop the blade well within the safety zone that's being monitored. Afterwards, you just press a button, reset the machine and it starts operating again. We haven't damaged the blade, we haven't cut the operator, and he can resume working straightaway."
It's been the Kiwi way – a good team of people with real smarts who have gone from an idea to a genuine commercial product in two years”
Guardian is a global product
After developing and testing a prototype over two years, kanDO's first commercial Guardian Bandsaw was installed in Auckland Meat Processors' Otahuhu plant in April 2017. There have been no accidents or injuries.
Auckland Meat Processors are taking two more machines, and three have been installed in processing plants in Australia. Brown says kanDO is actively marketing the Guardian in New Zealand and Australia and is negotiating with distributors in Britain and the United States.
He says "it's a global product – anywhere a bandsaw is used - and we are solving a global problem. It's been the Kiwi way – a good team of people with real smarts who have gone from an idea to a genuine commercial product in two years."
The innovative kanDO was spun out of Industrial Research Limited (now Callaghan Innovation) in 2007 when the founders Keith Blenkinsopp and Brown wanted to commercialise automation technology. They worked together at Industrial Research in Parnell.
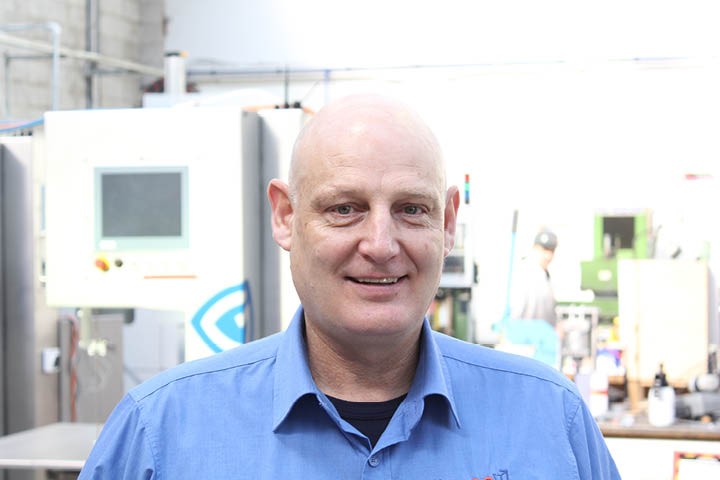
Mussel openers reduce costs
KanDO made automated mussel openers for Sanford in Havelock, Marlborough Sounds, and North Island Mussel Processors in Tauranga capable of processing six tonnes of cooked mussels in an hour. These plants are the first fully automated mussel processing factories in the world for half shell mussels and significantly reduce processing costs.
With a staff of 14, kanDO, developed a 360 degree vision inspection system for Villa Maria to check for faults in the wine labels which had been attached to the bottles; a number of systems for infant formula production lines to make sure the can and scoop are compliant with the rigorous quality standards for this product, and a system to inspect bottles for faults.
In Doha, kanDO designed a 28m tall street lighting pole capable of withstanding the harsh environmental conditions of a desert country. At the same time, kanDO developed an automated control system to lower the overhead lighting beam to a more serviceable height of 1m off the ground. More than 200 of the decorated light poles will line the Doha airport highway.